Innovations in Cleanroom Wall and Ceiling Materials
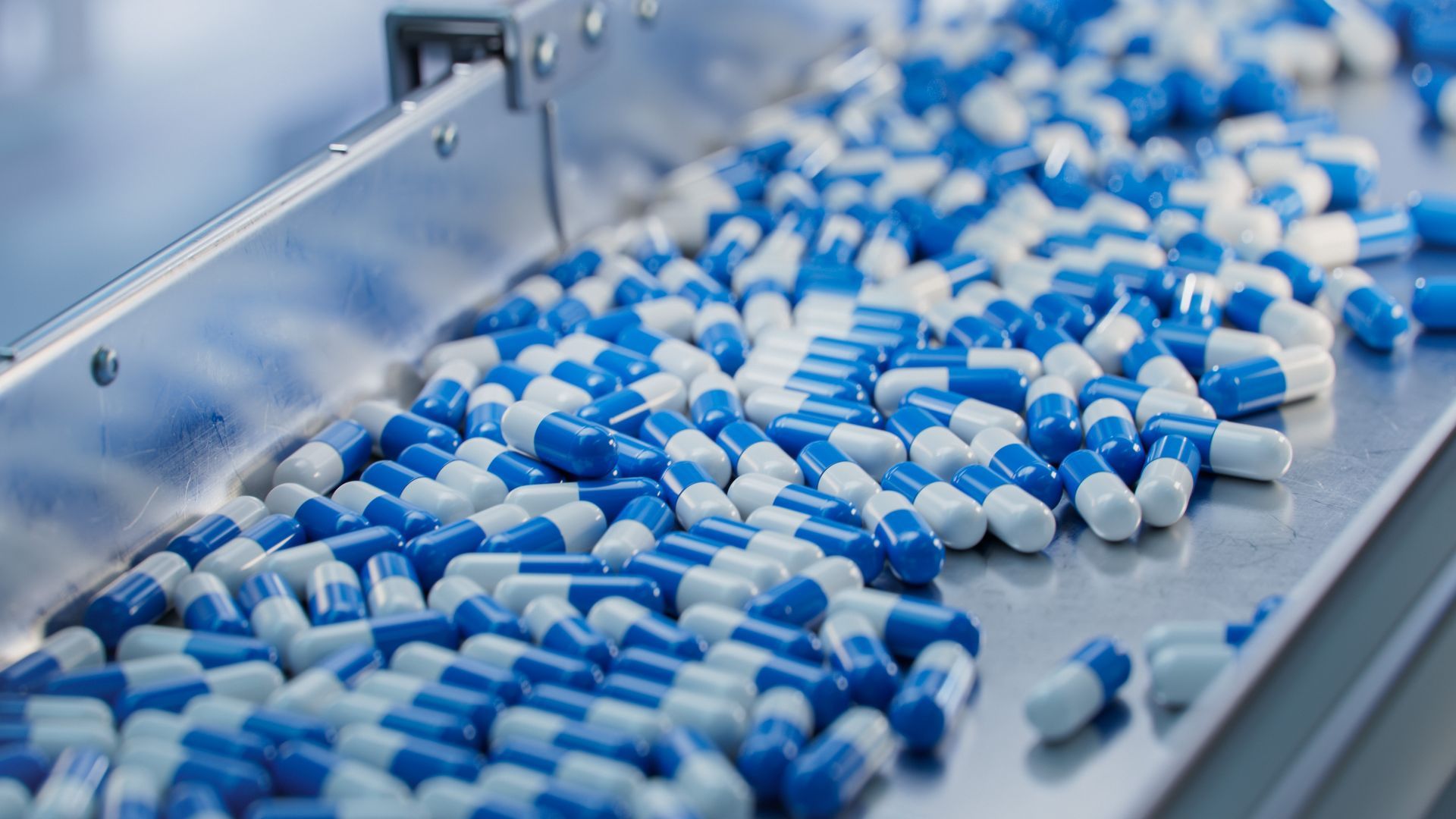
Introduction
Cleanrooms are environments that require stringent control over airborne particles, temperature, humidity, and other factors to ensure product quality, safety, and operational effectiveness. The materials used for cleanroom walls and ceilings are vital in maintaining cleanliness, structural integrity, and performance in highly regulated environments such as pharmaceuticals, biotechnology, electronics manufacturing, and aerospace.
Over time, innovations in cleanroom wall and ceiling materials have significantly advanced in response to evolving regulatory demands, sustainability needs, and operational efficiency. This article delves into the most impactful innovations in cleanroom wall and ceiling materials, highlighting new technologies, materials, and design concepts.
1. Introduction to Cleanroom Requirements
Cleanrooms are classified based on the level of particulate contamination they can tolerate. The materials used for the walls and ceilings in these rooms are expected to meet specific criteria that ensure optimal cleanliness and safety. These criteria include:
- Non-porosity: Walls and ceilings should be smooth and resistant to particle accumulation.
- Cleanability: Materials must be easy to clean, durable, and resistant to wear.
- Durability: Resistance to physical damage, chemicals, and thermal stress is critical.
- Fire resistance: Fire safety is crucial in highly regulated environments.
- Energy efficiency: Cleanroom materials must contribute to energy-saving solutions, especially with high operational costs.
2. Key Innovations in Cleanroom Wall Materials
Innovations in wall materials primarily focus on improving functionality, sustainability, and ease of installation. Below are some of the key innovations:
a. Modular Cleanroom Wall Systems
- Design Flexibility: Modular systems consist of pre-fabricated panels made from various materials, including metals, composites, and plastics. This modular approach allows for fast and easy construction, customization, and upgrades.
- Easy Maintenance: The modularity of the panels makes it easier to replace or adjust sections of the walls without disrupting the entire cleanroom operation.
- Integrated Features: Some modular systems feature integrated components like lights or airflow management systems.
b. High-Performance Coatings
- Anti-Microbial Coatings: These coatings help prevent the growth of harmful microorganisms on the surface, a critical feature in environments such as pharmaceuticals and food processing.
- Low-VOC Paints: Low volatile organic compound (VOC) paints improve air quality by releasing fewer harmful chemicals into the environment, contributing to cleaner air in the controlled environment.
- Enhanced Durability: These coatings improve the resistance of cleanroom surfaces to chemicals, moisture, and physical impact.
c. Composites and Hybrid Materials
- Fiberglass Reinforced Panels (FRP): FRP provides a smooth, durable, and resistant surface that is easy to clean, making it ideal for cleanroom environments.
- Hybrid Materials: Combining multiple materials (e.g., metals and plastics) allows for greater flexibility in achieving the desired balance of strength, durability, and ease of maintenance.
3. Innovations in Cleanroom Ceiling Materials
Ceilings in cleanrooms serve multiple functions, from supporting air filtration systems to ensuring uniform air circulation. Some innovations in ceiling materials include:
a. Suspended Ceiling Systems
- Improved Grid Systems: Modern suspended ceiling grids are designed with tight seals to reduce the accumulation of dust and particulate matter.
- Lightweight and Fire-Resistant Materials: Ceiling panels made from metals or composites offer better fire resistance and longer-lasting performance while maintaining ease of maintenance.
- Flexibility in Installation: Suspended ceilings offer flexibility in concealing electrical wiring, ducts, and other essential systems without compromising the cleanroom’s functionality.
b. Integrated Lighting and Air Filtration Systems
- Airflow Optimization: Integrated ceiling designs allow for the seamless incorporation of high-efficiency particulate air (HEPA) filters, ensuring that clean air is continually supplied to the room.
- Streamlined Maintenance: The integration of lighting and filtration systems into the ceiling minimizes the need for separate installations, reducing the risk of contamination and simplifying maintenance.
c. Thermal Insulation Materials
- Aerogels and Composites: Advanced thermal insulation materials such as aerogels help maintain consistent temperatures and reduce energy consumption. These materials are highly efficient at preventing heat transfer, contributing to better temperature control and reduced energy costs.
- Condensation Control: Proper insulation materials help prevent condensation on ceiling surfaces, which could lead to contamination in sensitive cleanroom environments.
4. Sustainability and Energy Efficiency
As sustainability becomes a primary focus, cleanroom designs are evolving to incorporate energy-efficient materials and environmentally friendly practices.
a. Energy-Efficient Materials
- Reflective Foils and Aerogels: These materials provide superior insulation, reducing the need for heating and cooling systems while maintaining temperature stability.
- Smart Materials: Thermochromic or photochromic materials that respond to temperature or light conditions can further optimize energy consumption and reduce operational costs.
b. Recyclable Materials
- Eco-Friendly Composites: Many new cleanroom materials are designed to be recyclable, reducing waste generated during construction and operation.
- Green Certifications: Manufacturers are developing materials that meet sustainability certifications, contributing to cleaner construction practices and helping companies achieve their green building goals.
5. Future Trends and Research Directions
Ongoing research in material science and cleanroom design is focused on enhancing the performance, sustainability, and cost-efficiency of cleanroom environments.
a. Smart Cleanroom Technologies
- Sensors and Monitoring: The integration of smart sensors into walls and ceilings will allow for real-time monitoring of temperature, humidity, and particle counts. This technology will enable automated adjustments, improving the efficiency of cleanroom operations.
- Predictive Maintenance: With the help of machine learning and data analytics, cleanroom wall and ceiling systems will be able to predict wear and tear, enabling more efficient maintenance schedules.
b. Advanced Airflow Systems
- Dynamic Airflow Control: Research into dynamic airflow systems aims to enhance air circulation and particle removal based on real-time conditions, reducing energy consumption and improving the overall cleanliness of the room.
- Modular Airflow Management: New innovations in modular air filtration and ventilation systems are designed to be integrated into both walls and ceilings, offering better control over airflow distribution.
Conclusion
Innovations in cleanroom wall and ceiling materials have significantly advanced over the years, driven by the need for higher performance, greater sustainability, and operational efficiency. From modular cleanroom wall systems to advanced ceiling panels with integrated air filtration and lighting, these innovations contribute to better control over the cleanroom environment and ensure compliance with stringent regulations. As the demand for cleaner, more sustainable, and more efficient cleanrooms grows, it is likely that further advancements will continue to reshape the way cleanroom walls and ceilings are designed and constructed, making these environments even more adaptable and effective in meeting the needs of various industries.
The growing focus on energy efficiency, smart technologies, and recyclable materials indicates that the future of cleanroom construction will prioritize sustainability without compromising on performance, safety, or cleanliness.
Read more: All about Cleanrooms : The Ultimate Guide
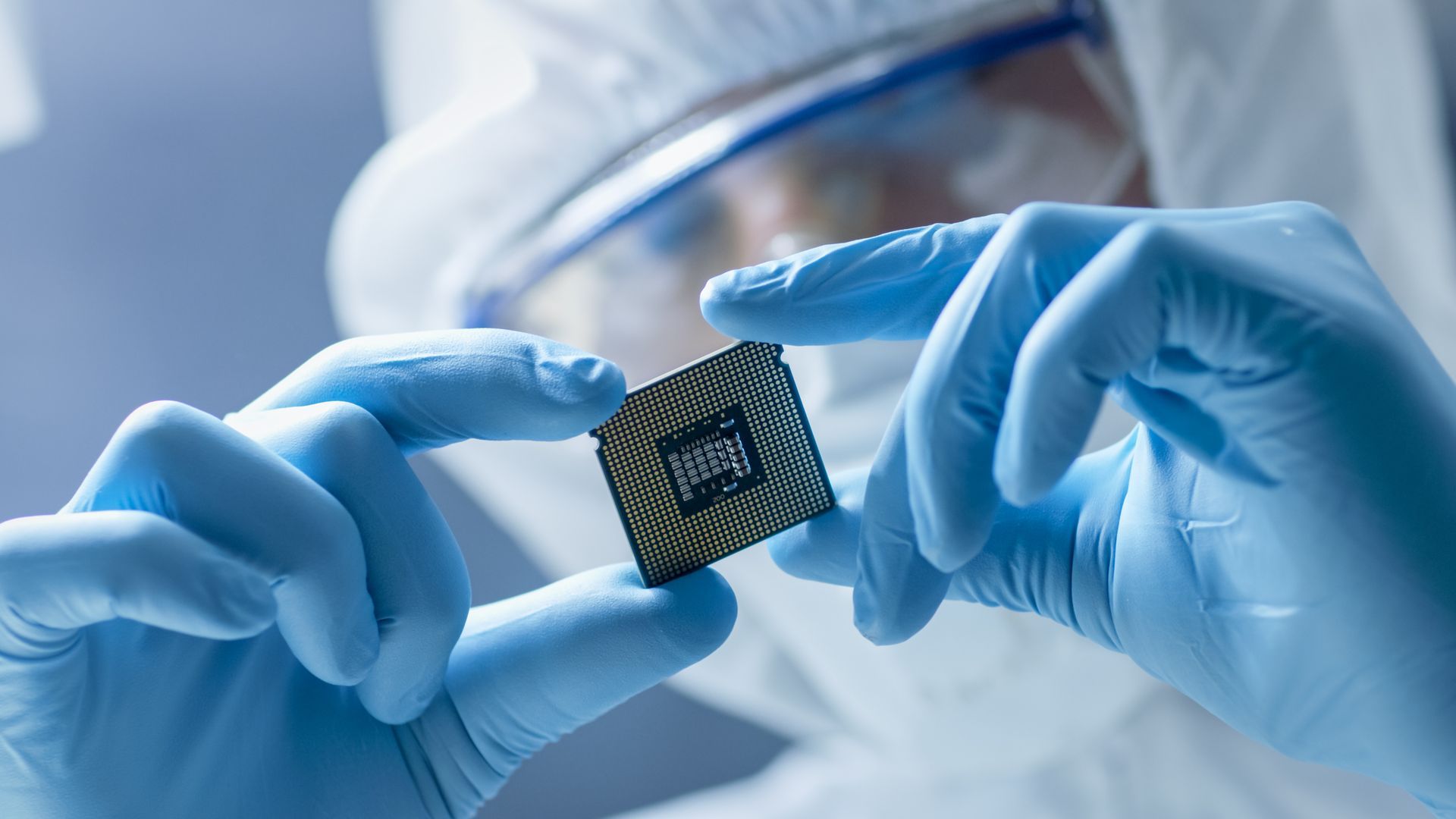
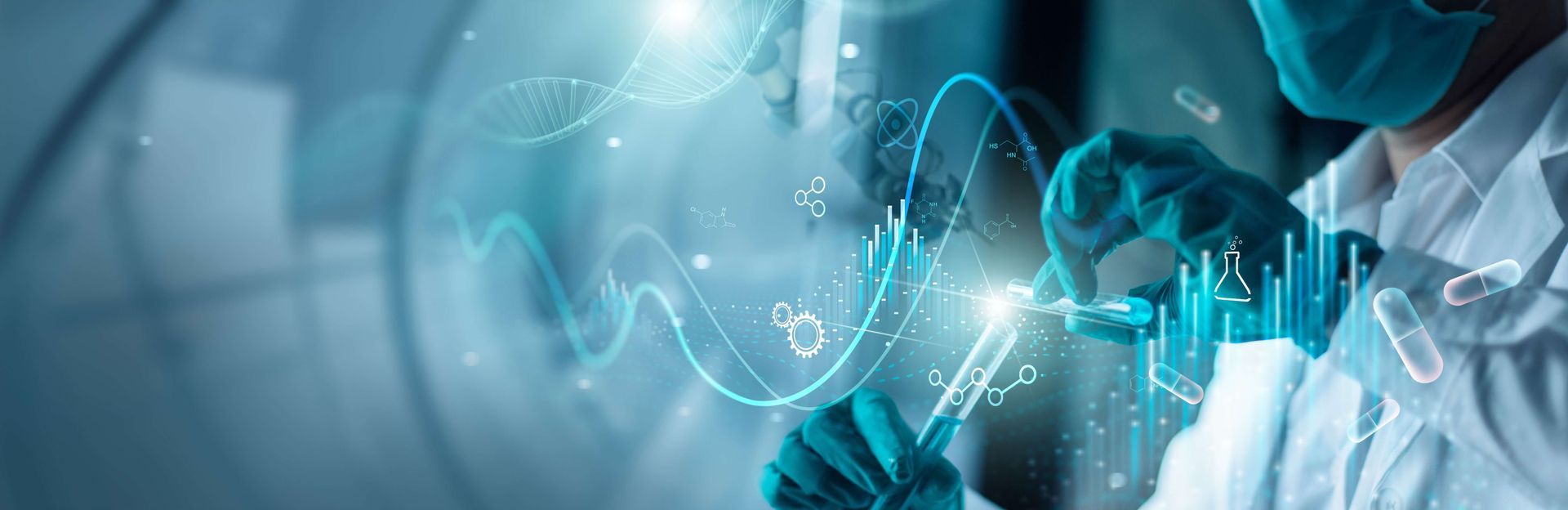