Managing Humidity and Temperature in Cleanrooms
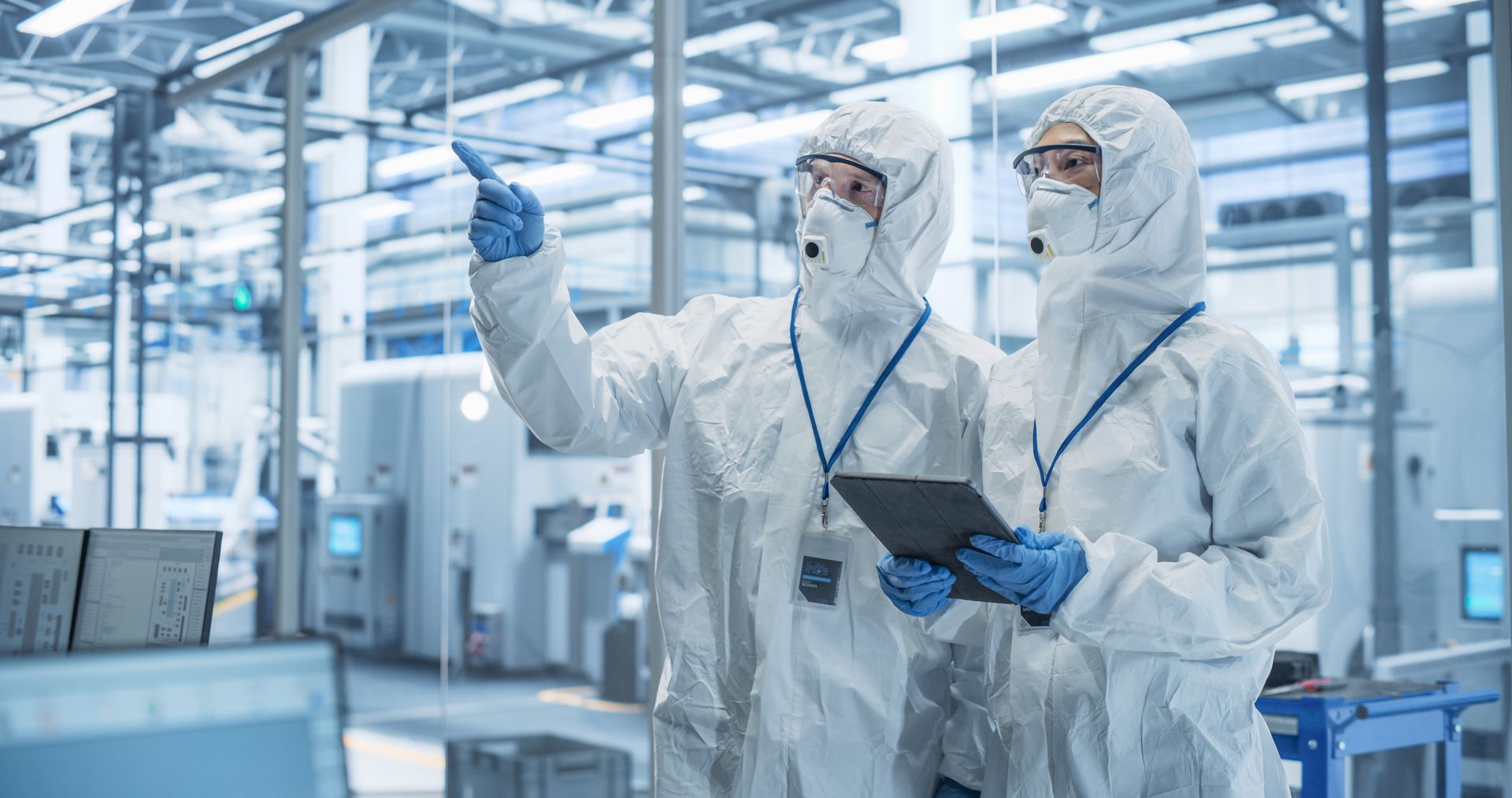
Introduction
Cleanrooms are critical environments that must adhere to stringent contamination control standards, primarily to protect the integrity of sensitive processes and products. In industries like pharmaceuticals, biotechnology, aerospace, semiconductor manufacturing, and healthcare, even the smallest contaminant can have a devastating effect on product quality, safety, and regulatory compliance. While particle contamination is the most commonly discussed issue in cleanroom design, managing environmental factors such as humidity and temperature is equally essential for maintaining the desired cleanroom performance.
Humidity and temperature directly impact both the cleanliness and the performance of processes within the cleanroom, influencing not only the integrity of products but also the comfort and safety of the personnel working in these controlled environments. Maintaining precise control over these factors is therefore crucial to achieving optimal cleanroom conditions.
This article will explore the role of humidity and temperature in cleanroom management, the risks associated with improper control of these factors, and the strategies and technologies used to regulate temperature and humidity within cleanrooms.
The Role of Humidity and Temperature in Cleanroom Performance
In cleanrooms, temperature and humidity affect both the physical properties of materials and the behavior of airborne particles. Each of these factors is tightly regulated to ensure that the cleanroom maintains its classification and that processes are completed without interruption or contamination.
Temperature Control
Temperature control in cleanrooms is typically dictated by the processes that occur within the environment. For instance, the temperature may need to be precisely regulated in areas such as pharmaceutical compounding, semiconductor fabrication, or aerospace testing, where even slight fluctuations can lead to undesirable outcomes.
- Impact on Chemical Reactions: In cleanrooms where chemicals are used in manufacturing processes or research, temperature plays a critical role in the efficiency and consistency of chemical reactions. In pharmaceutical production, for example, the temperature must be controlled to ensure that drug compounds are mixed, stored, and processed at optimal temperatures, avoiding any degradation or loss of potency.
- Impact on Equipment: Many cleanrooms, particularly those used in semiconductor fabrication and electronics manufacturing, contain sensitive equipment that operates under strict temperature conditions. Equipment can fail or perform poorly if subjected to temperatures that are too high or too low, leading to potential damage to the machinery and compromising product quality.
- Thermal Expansion: In environments that deal with sensitive instruments, such as aerospace testing cleanrooms, precise temperature control is necessary to prevent thermal expansion or contraction of materials that could affect measurement accuracy, structural integrity, or functionality.
- Human Comfort: The temperature in cleanrooms also affects the comfort and productivity of the personnel. If the temperature is too high, workers may experience fatigue, while temperatures that are too low can lead to discomfort or even impair cognitive performance. Striking a balance between process requirements and worker comfort is essential.
Humidity Control
Humidity management is equally critical in maintaining the quality of processes and products in a cleanroom. Humidity levels—defined by the amount of water vapor present in the air—are crucial for several reasons:
- Impact on Electrostatic Discharge (ESD): In cleanrooms dedicated to semiconductor manufacturing or electronics assembly, static electricity can wreak havoc on sensitive components. High humidity levels can help dissipate electrostatic charges by increasing the conductive properties of the air, thus reducing the risk of ESD damage.
- Microbial Growth and Contamination: In pharmaceutical or healthcare cleanrooms, where sterile conditions are required, humidity must be tightly controlled to prevent the growth of mold, bacteria, or other microorganisms. High humidity levels can create favorable conditions for microbial growth, while very low humidity can cause dry air that leads to particles and contaminants being more easily carried through the air.
- Material Properties: In industries such as aerospace or biotechnology, humidity can impact the physical properties of materials, such as polymers, adhesives, or coatings. Excessive humidity can affect the curing process of certain materials, while too little humidity can cause brittleness or cracking.
- Worker Comfort and Health: Similar to temperature, improper humidity levels can affect the comfort and health of personnel. High humidity can cause discomfort, fatigue, and dehydration, while low humidity can lead to dry skin, respiratory problems, and increased susceptibility to colds and other illnesses.
The Risks of Improper Temperature and Humidity Control
Improper regulation of temperature and humidity in cleanrooms can lead to several problems:
- Product Contamination: High humidity can cause condensation, which can lead to contamination on surfaces, equipment, or products. This is particularly problematic in environments such as pharmaceutical manufacturing, where sterility is paramount. Excess moisture can also cause corrosion, potentially damaging sensitive instruments.
- Degradation of Product Quality: In some industries, temperature and humidity must be maintained within very tight tolerances. For example, in semiconductor manufacturing, even small temperature fluctuations can affect the performance of microchips, leading to failures in product yields. Similarly, in the pharmaceutical industry, improper storage conditions can cause chemical degradation of drugs, reducing their efficacy.
- Compromised Process Integrity: Certain cleanroom processes, such as drug compounding, semiconductor fabrication, or coating applications, rely on very specific temperature and humidity conditions. Deviations from these conditions can lead to defects or suboptimal results, thus undermining the integrity of the manufacturing process.
- Health and Safety Issues: For personnel working in cleanrooms, poorly managed temperature and humidity can create an unsafe environment. Low humidity can cause discomfort and dry out respiratory passages, increasing the risk of infections. High humidity, on the other hand, can increase the likelihood of mold growth, leading to health risks for cleanroom operators.
Managing Temperature and Humidity in Cleanrooms
Managing temperature and humidity in cleanrooms involves several key strategies, from selecting the appropriate HVAC (Heating, Ventilation, and Air Conditioning) systems to continuous monitoring and adjustment of conditions. Below are the best practices for controlling these variables:
1. HVAC Systems for Temperature and Humidity Control
Cleanrooms are typically equipped with specialized HVAC systems designed to maintain precise control over temperature and humidity levels. These systems can include:
- Air Handling Units (AHUs): These units are responsible for regulating the temperature and humidity of the incoming air. They use advanced filtration and dehumidification processes to ensure that the air entering the cleanroom is free of contaminants and at the desired conditions.
- Humidity Control Units: In addition to standard HVAC units, many cleanrooms are equipped with dehumidifiers or humidifiers that can adjust the moisture levels in the air. These systems often use advanced sensors to measure humidity and make automatic adjustments to keep it within acceptable ranges.
- Temperature Control Units: Depending on the cleanroom’s requirements, temperature control units such as chillers, heating coils, and thermal storage systems can be used to regulate the temperature. These systems can be integrated with the cleanroom’s air handling system for precise temperature management.
2. Continuous Monitoring
To ensure that temperature and humidity remain within the acceptable range, continuous monitoring is crucial. Cleanroom environments are typically equipped with temperature and humidity sensors that constantly track these variables. Data from these sensors is sent to a central control system, where it is analyzed and used to make real-time adjustments to the HVAC system. Many modern systems allow for automated adjustments based on preset parameters.
Sensors and monitoring systems must be regularly calibrated to ensure their accuracy. These monitoring systems also help in maintaining compliance with regulatory standards by providing reliable data for audits and inspections.
3. Environmental Control Standards
The specific temperature and humidity levels that must be maintained in a cleanroom depend on the cleanroom's classification, the type of work being performed, and the standards set by regulatory agencies. For instance:
- ISO Class 1 to Class 5 Cleanrooms: These cleanrooms require extremely tight control over both temperature and humidity, often in the range of 18°C to 22°C (64°F to 72°F) for temperature, and 30-60% relative humidity for humidity. These standards ensure that the cleanroom environment remains stable for sensitive production processes, such as semiconductor fabrication or high-grade pharmaceutical manufacturing.
- Pharmaceutical Cleanrooms: The temperature and humidity levels in pharmaceutical cleanrooms are often defined by GMP (Good Manufacturing Practices) standards. These facilities may need to maintain a temperature range of 18°C to 25°C (64°F to 77°F) and a relative humidity range of 30% to 65%.
4. Redundancy and Backup Systems
Given the critical nature of temperature and humidity control, cleanrooms often incorporate redundant systems to ensure that any failure in the primary system does not compromise cleanroom conditions. These can include backup power supplies, redundant air handling units, and fail-safe systems that alert operators to any deviations from acceptable conditions.
5. Routine Maintenance
To ensure the ongoing performance of HVAC systems and to avoid costly breakdowns, routine maintenance is essential. This includes regular checks of air filters, humidity control systems, and temperature control units, as well as cleaning and servicing of sensors and other monitoring equipment.
Conclusion
Managing temperature and humidity in cleanrooms is essential for maintaining product quality, process integrity, and personnel safety. These factors affect not only the physical environment but also the behavior of particles, chemicals, and materials, all of which are vital to cleanroom operations. The use of advanced HVAC systems, continuous monitoring, and adherence to industry-specific environmental standards ensures that cleanrooms maintain the desired conditions at all times. By implementing proper temperature and humidity control measures, cleanroom operators can safeguard the success of their processes, enhance operational efficiency, and meet regulatory compliance standards.
Read more:
All About Cleanrooms - The ultimate Guide
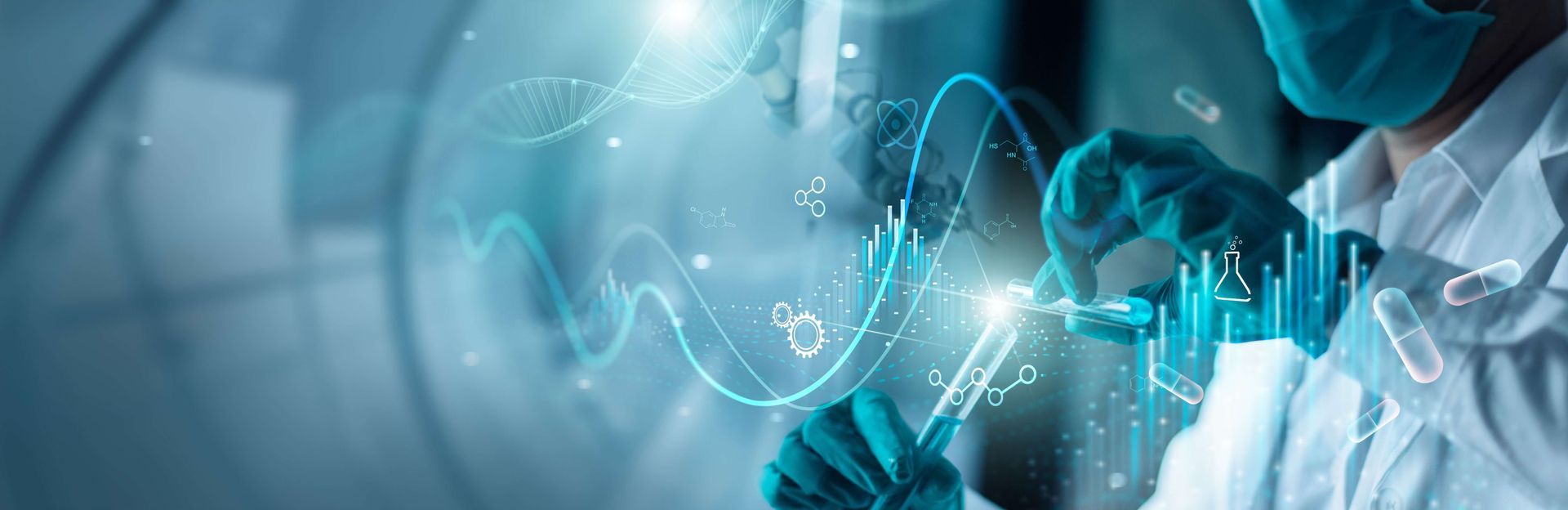
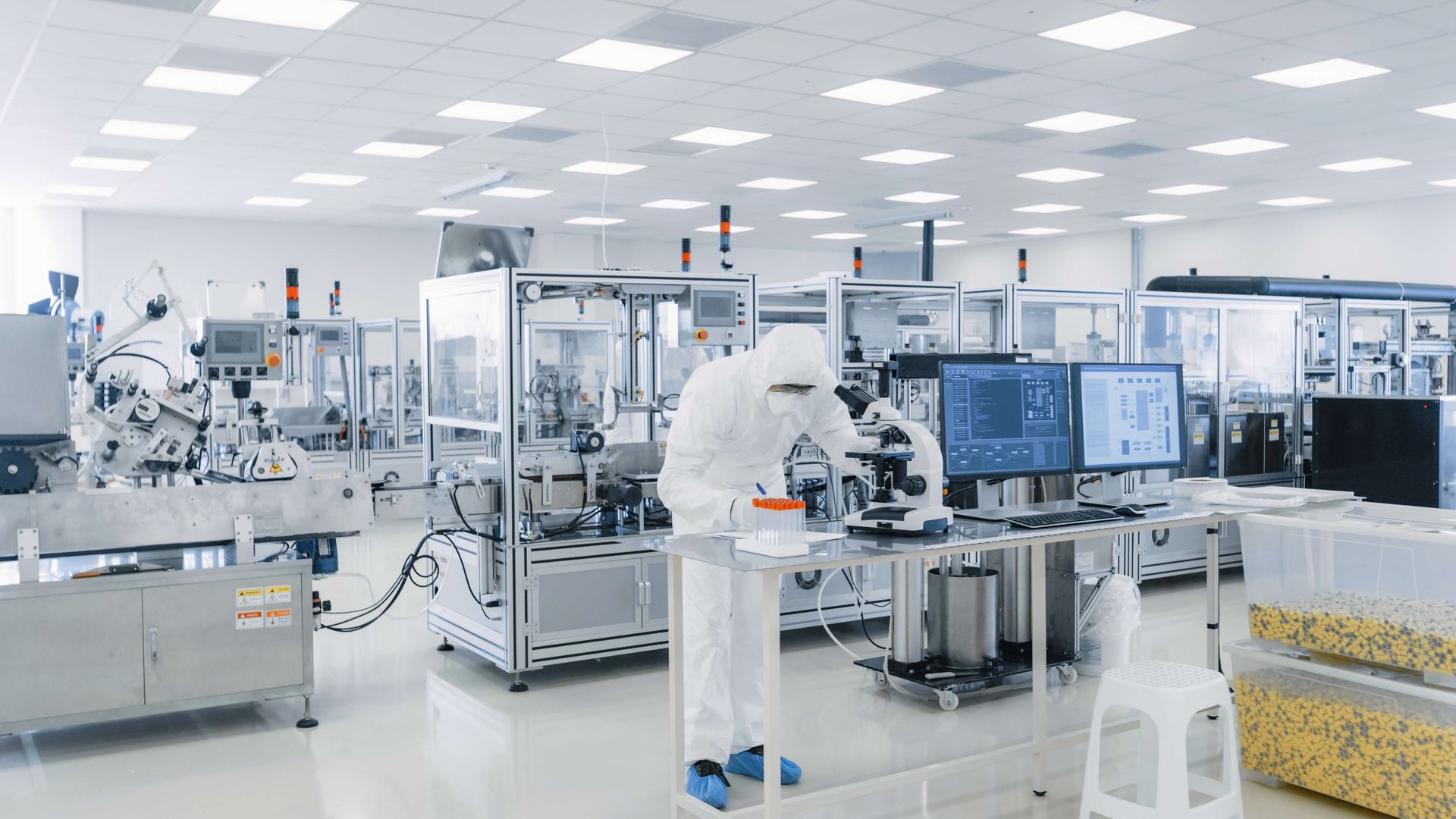