The Importance of Air Flow Patterns in Cleanroom Design
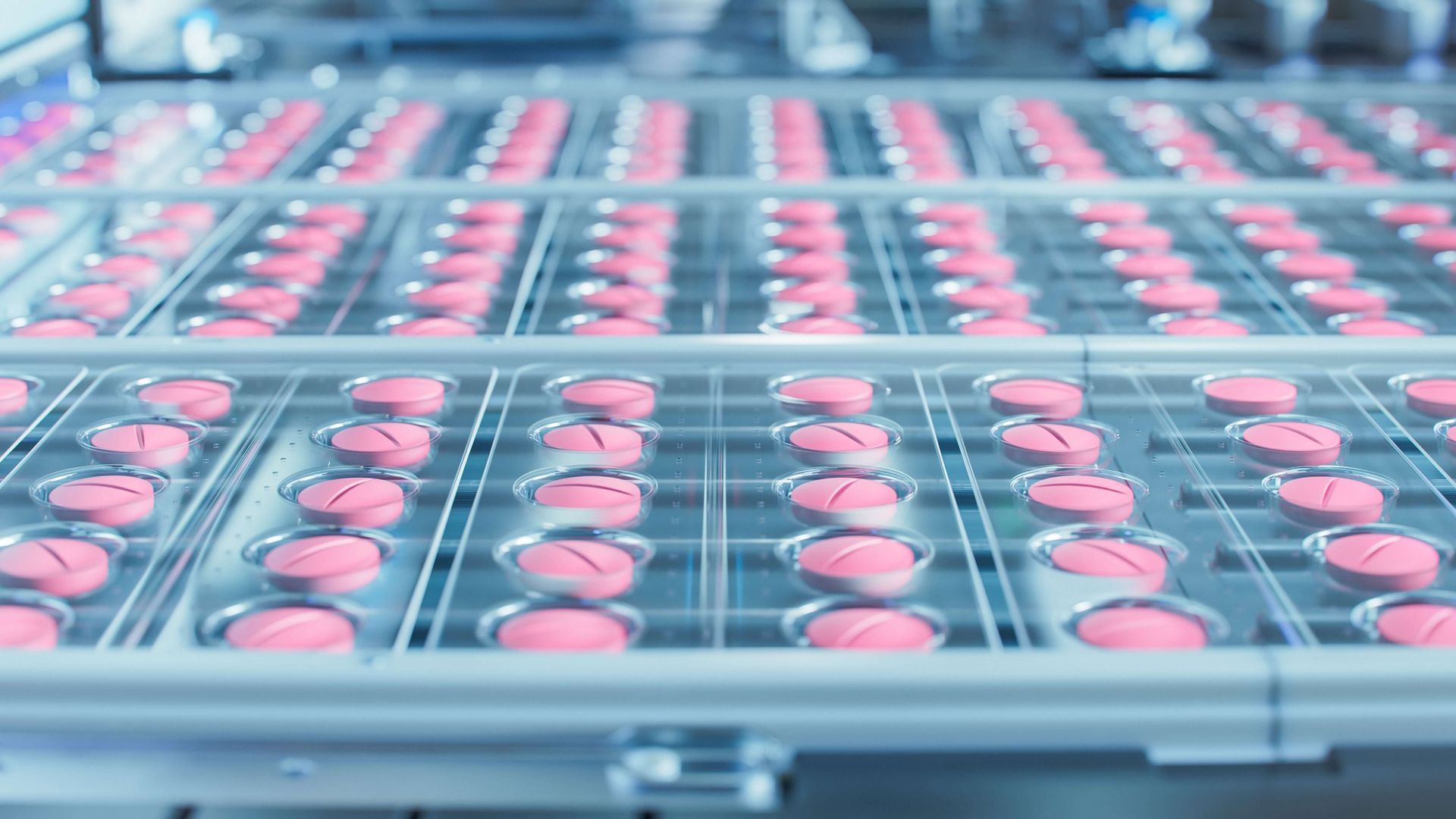
Introduction
Cleanrooms are controlled environments designed to minimize contamination risks and maintain the highest standards of cleanliness. Industries such as pharmaceuticals, biotechnology, aerospace, semiconductor manufacturing, and medical devices rely on these spaces to ensure the safety, efficiency, and quality of their processes and products. One of the most critical aspects of cleanroom design is the management of airflow patterns.
Proper airflow patterns ensure that particulate contamination is minimized, clean air is evenly distributed, and the cleanroom environment remains effective in preventing contamination.
In this article, we will explore why air flow patterns are so important in cleanroom design, how they influence contamination control, and the strategies used to optimize air flow in cleanrooms to meet stringent industry standards.
Understanding Cleanroom Air Flow
Air flow patterns in a cleanroom refer to how air circulates throughout the space, from its entry into the room to its exit. The flow of air directly impacts how contaminants—such as particles, dust, or microorganisms—are carried and removed from the environment. Airflow also affects the room's pressure, temperature, humidity, and, ultimately, its classification according to standards like ISO 14644-1.
The main goal of airflow design in a cleanroom is to ensure that particles generated within the cleanroom, whether from equipment, materials, or personnel, are swiftly removed without contaminating the workspace or settling onto sensitive products. Proper air flow patterns achieve this by directing contaminated air out of the cleanroom, replacing it with clean, filtered air.
The Role of Airflow in Cleanroom Contamination Control
Contamination control is one of the core functions of cleanroom airflow design. In cleanrooms, contamination can originate from several sources:
- Personnel: Workers in cleanrooms, even with protective gowns and gear, can shed skin cells, hair, and particles. Proper airflow ensures that these particles are removed from the workspace before they have a chance to settle on surfaces or products.
- Equipment and Materials: Cleanroom equipment, machinery, and materials may also generate particulate contamination. Efficient airflow ensures that particles generated by these sources are quickly carried away from sensitive areas.
- External Contamination: Airflow patterns can also help control the ingress of contaminants from external sources, such as ventilation systems or the air outside the cleanroom. Ensuring a proper differential pressure between the cleanroom and adjacent areas reduces the risk of contaminants entering the cleanroom from uncontrolled spaces.
By designing air flow to remove particles from critical areas efficiently, cleanroom designers help ensure the integrity and sterility of the products being manufactured or processed.
Types of Airflow Patterns in Cleanroom Design
There are several types of airflow patterns commonly used in cleanroom design, each of which plays a different role in particle control and cleanroom performance:
1. Laminar Flow
Laminar flow is one of the most commonly used airflow patterns in cleanrooms, particularly in environments where the risk of contamination is high, such as pharmaceutical manufacturing or semiconductor fabrication.
In laminar flow, air moves in parallel layers with minimal disruption between them. This flow pattern is characterized by smooth, unidirectional movement, which helps sweep contaminants away from sensitive areas. Laminar flow can be horizontal or vertical, depending on the cleanroom's design.
- Vertical Laminar Flow: In vertical laminar flow, air is drawn from the ceiling and moves downward toward the floor. This type of flow is most common in cleanrooms where sensitive products or processes are located near the floor, such as in assembly areas or packaging areas. The air is typically filtered through HEPA (High-Efficiency Particulate Air) or ULPA (Ultra-Low Penetration Air) filters before being introduced into the cleanroom to ensure the highest possible level of air purity.
- Horizontal Laminar Flow: In horizontal laminar flow, air is drawn into the cleanroom from one side and moves horizontally across the room, typically towards an exhaust vent or filtration system. This design is often used in areas where large equipment or workbenches are placed along one side of the room.
Advantages of Laminar Flow:
- Effective in sweeping airborne particles away from critical areas.
- Minimizes turbulence that could disturb the particulate settling in sensitive areas.
- Provides consistent air distribution across the cleanroom, ensuring all areas receive a uniform level of air cleanliness.
Considerations:
- It requires precise control over airflow to ensure that particles are continually removed.
- Potential inefficiency in rooms with a large number of obstructions or complex layouts, as airflow might not reach all areas efficiently.
2. Turbulent Flow
Turbulent flow, on the other hand, is less controlled than laminar flow and results in chaotic air movement. This flow pattern is typically found in environments where contamination is less critical, such as in low-ISO cleanrooms (ISO 7 and 8), or in support areas like storage rooms.
While turbulent flow is less efficient at removing particles from critical areas, it can still play an important role in larger, more open spaces or less-sensitive parts of the cleanroom. The air will still eventually be filtered, but the air moves more erratically compared to laminar flow.
Advantages of Turbulent Flow:
- Easier to implement in larger or less critical areas of a cleanroom.
- Can be used in non-production areas where contamination control requirements are less stringent.
Considerations:
- Less effective at maintaining uniform cleanliness in areas where contamination is critical.
- Can lead to stagnant air pockets, where particles can accumulate.
3. Unidirectional Flow
Unidirectional flow, often used in combination with laminar flow, refers to a specific type of air circulation where the airflow is directed in one consistent direction. Unidirectional airflow is designed to ensure that contaminants are constantly being directed out of the cleanroom, and it is typically used in spaces like clean benches, isolators, or controlled workstations.
This airflow system combines laminar flow principles with the continuous movement of air to create a highly controlled, sterile environment in areas where very high standards are required.
Advantages of Unidirectional Flow:
- Perfect for maintaining a highly sterile environment for critical processes such as drug compounding or electronics manufacturing.
- Reduces the potential for cross-contamination between workers or workstations.
Considerations:
- Requires careful design and placement of air supply and exhaust systems.
- Generally not suitable for large-scale production areas due to its focused nature.
The Importance of Airflow Patterns for ISO Cleanroom Classes
Cleanroom standards, such as those set by the International Organization for Standardization (ISO 14644-1), define the cleanliness of a room based on the number of particles per cubic meter at specific sizes. As the cleanroom class decreases (i.e., from ISO 5 to ISO 8), the acceptable particle count increases, which directly impacts airflow requirements.
- ISO Class 1 to Class 5: These classes require highly efficient airflow systems, including laminar flow and unidirectional airflow. The air must be filtered multiple times (often through HEPA or ULPA filters) to remove particles, and the air must be delivered in a controlled, uniform manner to avoid turbulence and particle deposition. Cleanrooms of these classes are typically used for highly sensitive processes like semiconductor manufacturing, pharmaceuticals, and biotechnology.
- ISO Class 6 to Class 8: As the cleanliness standards become less strict, airflow systems can become less stringent, but they still need to ensure that contaminants are removed from critical areas. These classes are often found in industries like food packaging or less-sensitive assembly lines, where a less precise level of airflow is acceptable.
Key Considerations for Designing Airflow Patterns
When designing airflow patterns in a cleanroom, several factors need to be taken into account:
- Cleanroom Size and Layout: The size and layout of the cleanroom will influence how air flows through the space. For large rooms, multiple air handling units may be needed, and careful planning is required to ensure that airflow is evenly distributed across all critical areas.
- Personnel and Equipment Placement: The location of personnel and equipment will also influence air flow patterns. Workstations, machinery, and equipment should be positioned in such a way that they do not disrupt airflow or create turbulence that could lead to contamination.
- Airflow Velocity: The velocity of the airflow must be carefully regulated to avoid disturbing settled particles or causing turbulence that could affect contamination control. Too high a velocity can cause particulate movement, while too low a velocity may allow particles to settle back onto surfaces.
- Pressure Differentials: To ensure that contaminants do not enter the cleanroom, pressure differentials between the cleanroom and surrounding areas must be maintained. Positive pressure is typically used in cleanrooms to prevent the ingress of contaminated air from adjacent spaces.
- Filtration Systems: Filtration is a critical component of cleanroom airflow. Air entering and exiting the cleanroom must pass through high-efficiency filters, such as HEPA or ULPA, to ensure that airborne particles are removed before the air enters the cleanroom or exits to the environment.
Conclusion
Airflow patterns are a fundamental aspect of cleanroom design and performance. By ensuring that air circulates effectively, cleanrooms can maintain their cleanliness standards, protect product integrity, and prevent contamination from personnel, equipment, and external sources.
Whether utilizing laminar flow, turbulent flow, or unidirectional flow, the proper design of airflow systems is essential for meeting ISO classification requirements and creating a safe, sterile environment for sensitive processes and products. Cleanroom designers must carefully consider factors such as room layout, airflow velocity, personnel positioning, and filtration systems to achieve the best possible airflow design for their specific application.
Read more: All About Cleanrooms - The ultimate Guide
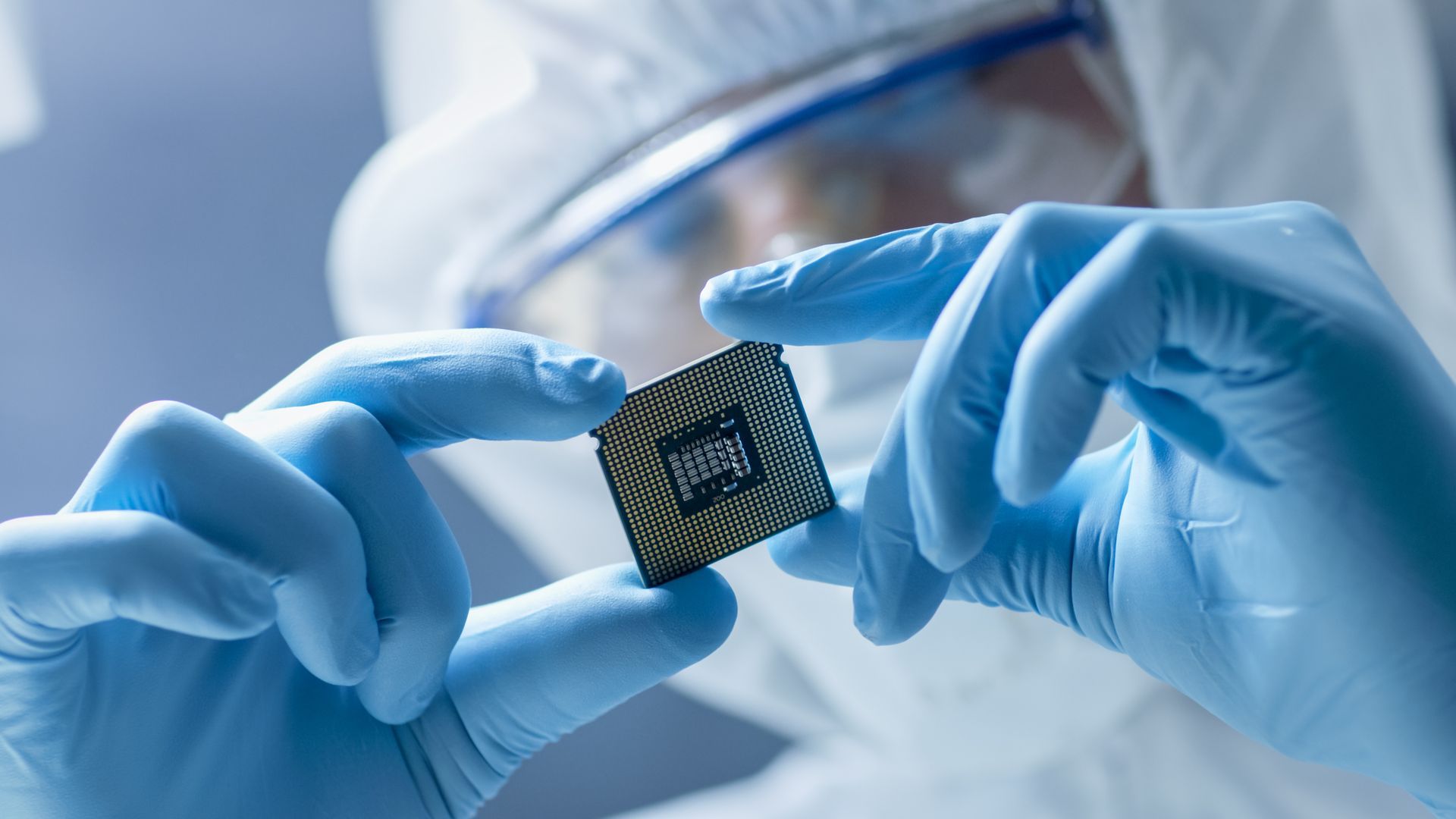
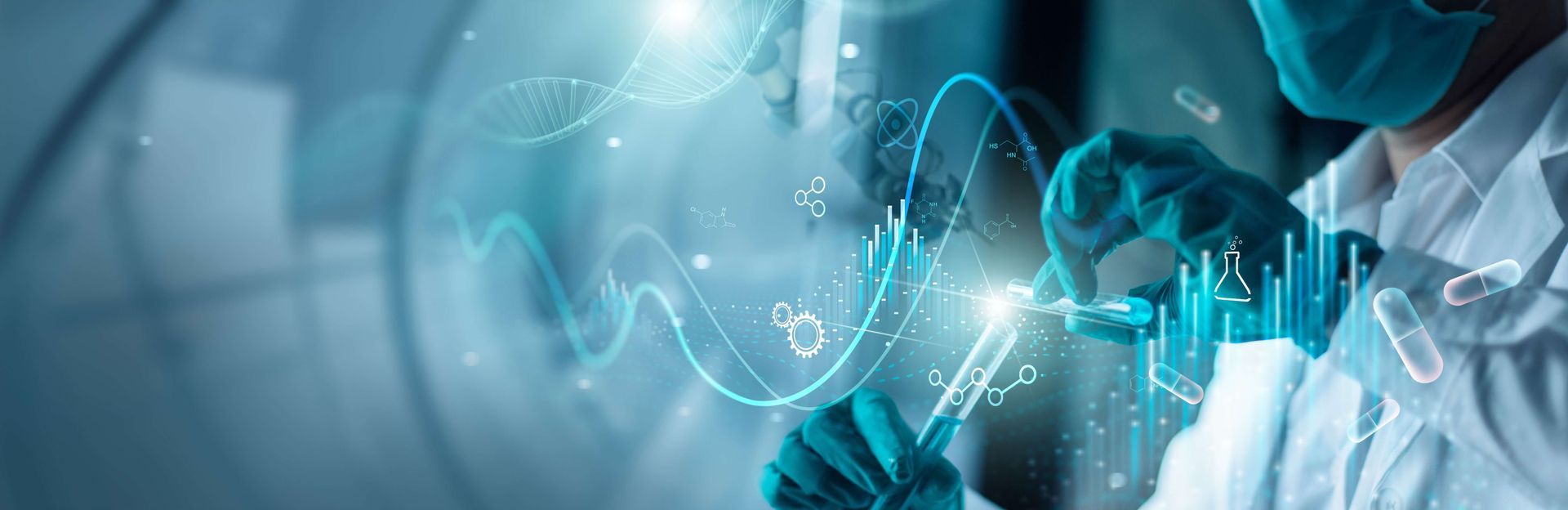