Cleanroom Furniture: Design and Material Selection

Introduction
In industries such as pharmaceuticals, biotechnology, semiconductor manufacturing, aerospace, and medical devices, maintaining a contamination-free environment is essential. Cleanrooms are critical spaces where environmental conditions must be meticulously controlled to prevent contamination from airborne particles, microorganisms, and other potential pollutants. The cleanliness of a cleanroom is often the determining factor in ensuring the quality and safety of sensitive products, research, or manufacturing processes.
While many cleanroom designs focus on elements like air filtration, temperature and humidity control, and gowning procedures, cleanroom furniture also plays a vital role in maintaining the integrity of the controlled environment. The design and material selection for cleanroom furniture are crucial considerations because they can influence how easily the room can be cleaned, the level of particle generation, and the overall functionality of the space.
In this article, we will dive into the importance of cleanroom furniture, factors influencing its design, and the best materials to use in cleanroom environments. We will explore how furniture design and material selection contribute to maintaining cleanliness, safety, and operational efficiency in cleanrooms.
The Role of Furniture in Cleanroom Environments
Cleanroom furniture includes a variety of items, such as workbenches, chairs, shelves, storage cabinets, carts, and other pieces used by personnel to support tasks in the controlled space. Furniture in cleanrooms is different from typical office or industrial furniture due to its unique demands. In cleanrooms, all furniture needs to be:
- Easily Cleanable: Furniture should not trap dust, particles, or microorganisms that could contaminate the cleanroom environment. Smooth, non-porous surfaces that are easy to clean and disinfect are essential.
- Particle-Free: Furniture in cleanrooms should generate as few particles as possible. Materials with low particle shedding are preferred to prevent the introduction of contaminants.
- Durable: Cleanroom furniture must withstand frequent cleaning, chemicals, temperature variations, and heavy usage while maintaining its functionality and structural integrity.
- Non-Reactive: Furniture materials should be non-reactive to chemicals and other substances used in cleanrooms. Some materials may react with cleaning agents or chemicals in ways that could lead to contamination or degradation.
- Safe and Ergonomic: The furniture design should support safe, comfortable working conditions for personnel. Ergonomic considerations are especially important for workers who may spend long hours in the cleanroom.
Key Considerations in Cleanroom Furniture Design
When designing cleanroom furniture, several factors need to be taken into account to ensure that the furniture supports the cleanroom’s primary functions while minimizing the potential for contamination:
1. Functionality and Layout
The design of the furniture should align with the specific processes carried out in the cleanroom. For example, in semiconductor fabrication, workbenches must be designed to support the delicate assembly and testing of microelectronic components, while in pharmaceutical cleanrooms, furniture must facilitate the handling and preparation of sterile drug formulations.
- Workbenches and Tables: The size, shape, and height of workbenches must be optimized for the tasks being performed. Work surfaces must be spacious enough to accommodate equipment and materials while allowing for easy access and movement.
- Shelving and Storage: Shelving and storage units should be designed to hold materials and equipment in an organized, easily accessible manner. Shelves and cabinets should have smooth, sealed surfaces to prevent dust and particle accumulation. Additionally, storage units may need to be specially designed to handle chemicals or hazardous materials in specific industries, like pharmaceuticals or biotechnology.
- Carts and Mobile Furniture: For flexibility and ease of movement, cleanroom carts and other mobile furniture are often used. These pieces must be easy to maneuver and clean and should be designed to reduce the potential for cross-contamination.
2. Material Selection
The choice of materials for cleanroom furniture is one of the most important factors in the design process. The materials must meet several stringent requirements, including being durable, easy to clean, non-reactive, and resistant to the harsh cleaning agents commonly used in cleanroom environments.
Some of the most common materials used in cleanroom furniture include:
1. Stainless Steel
Stainless steel is one of the most widely used materials for cleanroom furniture, particularly in workbenches, storage units, and equipment racks. It is valued for its durability, resistance to corrosion, and ease of cleaning. Stainless steel does not absorb contaminants, making it an ideal material for environments where cleanliness is paramount.
Advantages of Stainless Steel:
- Highly resistant to chemicals and corrosion
- Easy to clean and maintain
- Non-porous, preventing the absorption of contaminants
Considerations:
- Can be prone to scratching, which may allow particles to accumulate in the scratches
- Cold to the touch, which may be uncomfortable in some cleanroom settings
2. Aluminum
Aluminum is another popular material for cleanroom furniture. It is lighter than stainless steel but still offers many of the same benefits, such as durability, resistance to corrosion, and ease of cleaning.
Advantages of Aluminum:
- Lightweight and easy to handle
- Resistant to corrosion and rust
- Cost-effective compared to stainless steel
Considerations:
- Not as durable as stainless steel and may not withstand harsh chemicals as well
- Can be more prone to denting or bending under heavy use
3. Plastic and Polymer Materials
Plastic and polymer materials, such as polypropylene, polycarbonate, and high-density polyethylene (HDPE), are commonly used in cleanroom furniture, especially for shelves, drawers, and smaller storage units. These materials are lightweight, non-porous, and resistant to chemical corrosion.
Advantages of Plastic/Polymer Materials:
- Lightweight and cost-effective
- Resistant to chemicals and moisture
- Easy to clean and maintain
Considerations:
- May not offer the same level of durability and strength as metals like stainless steel
- May not provide adequate static protection for sensitive electronic work
4. Laminate Surfaces
Laminate surfaces are often used for work surfaces and countertops in cleanrooms. These surfaces can be made from materials such as phenolic resin or melamine, which provide a durable, non-porous, and easy-to-clean surface.
Advantages of Laminate Surfaces:
- Essential for electronics, semiconductor, and other ESD-sensitive environments
- Prevents the buildup of harmful static charges
Considerations:
- The effectiveness of antistatic coatings may degrade over time and with wear
- Can add to the overall cost of the furniture
5. ESD-Safe Materials
I
n cleanrooms where electrostatic discharge (ESD) could damage sensitive equipment, furniture must be designed to minimize static buildup. Furniture made from materials with antistatic or conductive properties, such as ESD-safe mats, chairs, and workstations, is critical in environments like semiconductor manufacturing.
Advantages of ESD-Safe Materials:
- Aesthetic appeal in non-critical areas
- Easy to work with and can be shaped into custom designs
Considerations:
- Porous and difficult to clean thoroughly in high-contamination risk areas
- Susceptible to warping or damage when exposed to moisture or chemicals
Specialized Cleanroom Furniture Designs
In addition to general furniture items like tables, chairs, and shelving, cleanroom environments may require specialized furniture for unique tasks or environments. Some of these include:
- ESD-Safe Workbenches: These workstations are equipped with special materials or coatings that prevent electrostatic charge buildup, which is vital for electronics and semiconductor manufacturing.
- Ergonomic Seating: Cleanroom chairs are designed for comfort and safety, particularly in settings where workers spend long hours. They often feature adjustable components and materials that minimize particle release while providing maximum support.
- Customizable Storage Units: Cleanroom storage units often feature specialized shelving, drawers, and compartments designed for easy cleaning, particle control, and optimal organization.
Conclusion
The design and material selection of cleanroom furniture are integral to the success of a cleanroom's operation. Choosing the right materials and ensuring furniture is functional, durable, and easy to clean are key factors that contribute to the overall cleanliness, safety, and efficiency of the environment. Whether opting for stainless steel for its durability, plastic for its versatility, or specialized materials for static control, the proper selection of materials can help mitigate contamination risks and improve worker comfort.
By considering factors such as particle generation, chemical resistance, and ergonomic needs, businesses can ensure their cleanroom furniture meets the highest standards and plays a critical role in maintaining a controlled, sterile environment conducive to the specific needs of their industry.
Read more: All About Cleanrooms - The ultimate Guide
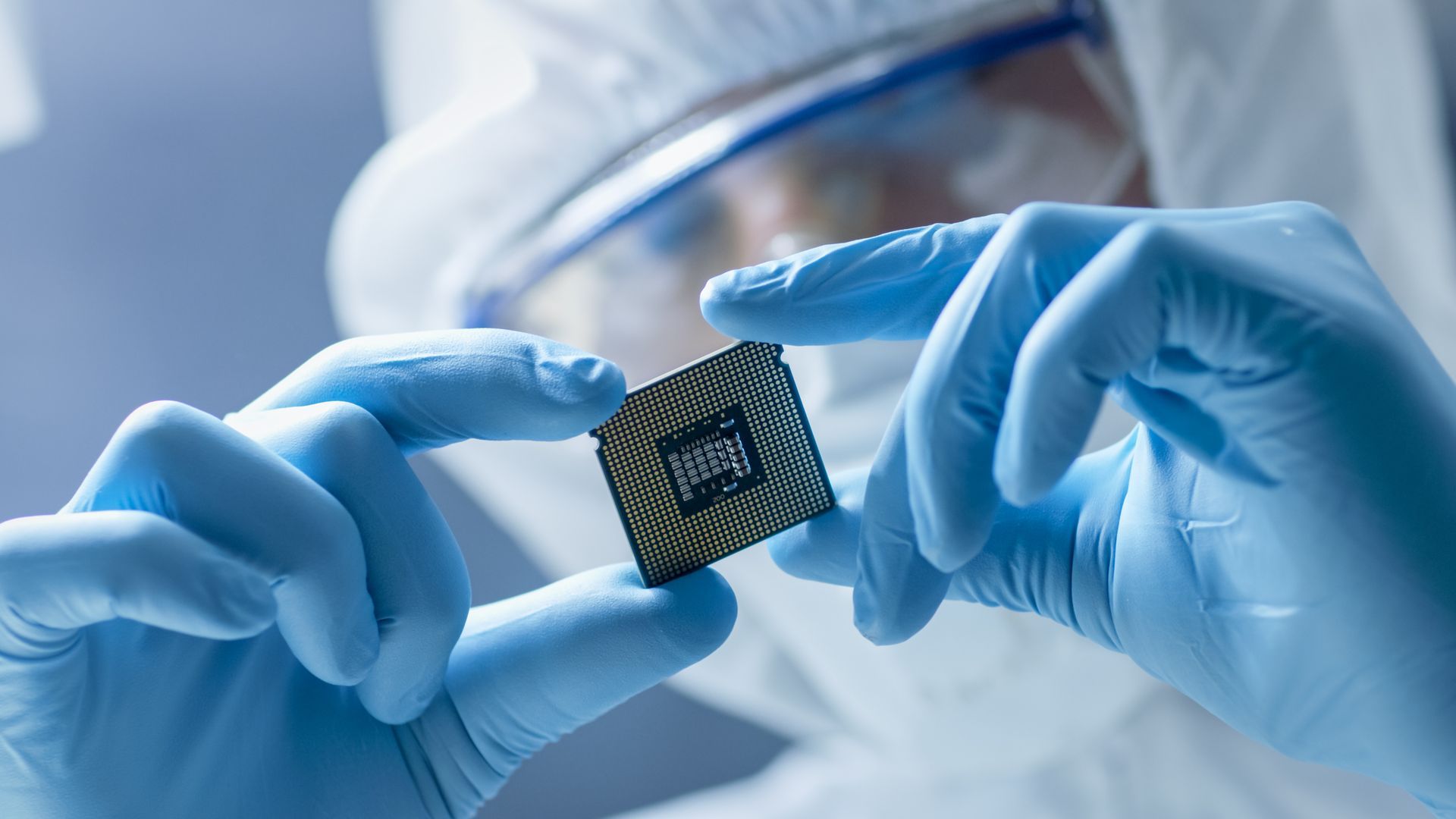
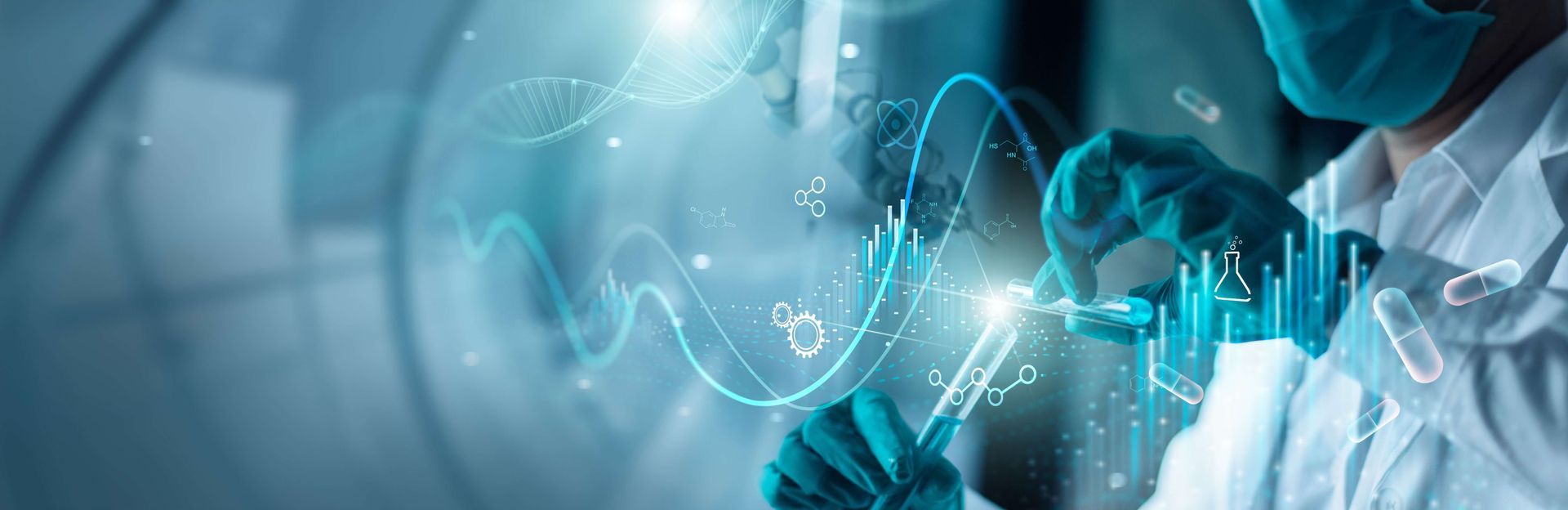